
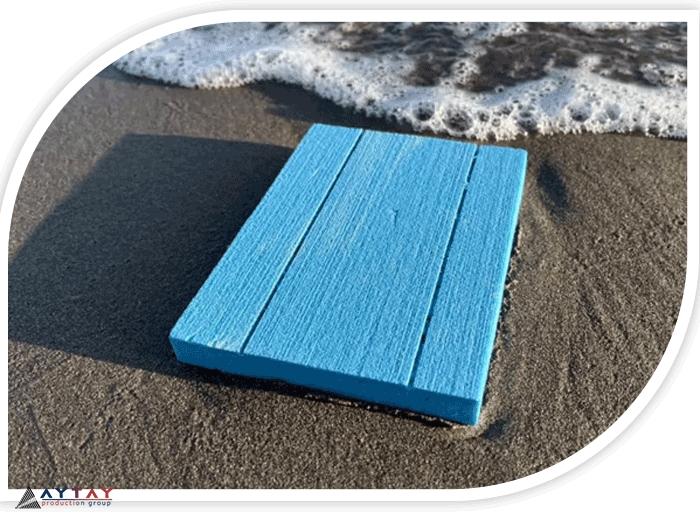
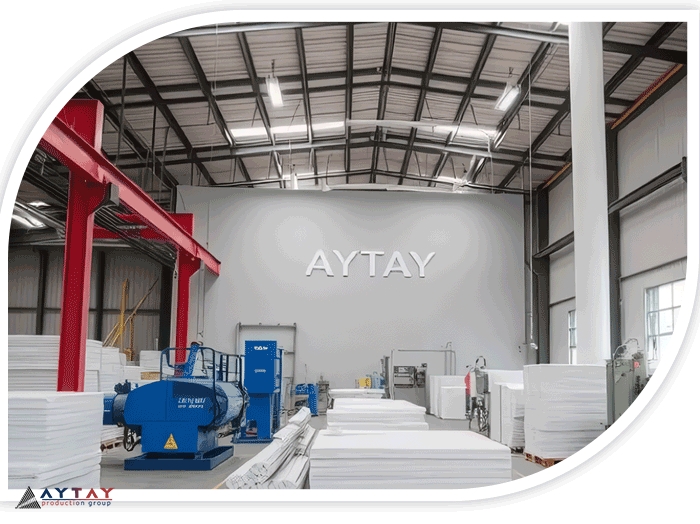
- Moisture Insulation (Moisture Absorption 0.2%): XPS foam, with its closed-cell structure, has very low moisture absorption. This feature makes the foam resistant to water and vapor penetration, preventing damage caused by moisture.
- Thermal Insulation (Thermal Exchange 0.003%): With a very low thermal conductivity coefficient, XPS foam acts as an effective thermal insulator. This feature helps reduce energy costs and maintain the internal temperature of buildings.
- Cooling Insulation (Subject of Chapter 19 of Iran's Building Code): This foam is also recognized as a cooling insulator and is designed according to Chapter 19 of Iran's National Building Regulations to perform optimally in various climatic conditions.
- High Compressive Strength (20 to 50 tons per square meter): XPS foam has high compressive strength, making it suitable for use in industrial and construction projects. This characteristic allows the foam to withstand heavy loads without deforming.
- Permissible Operating Temperature 50 to 75 degrees Celsius: This foam can perform well at operating temperatures between 50 and 75 degrees Celsius, making it ideal for use in various weather conditions.
- Antibacterial and Environmentally Friendly (Insect and Pest Resistance): The unique structure of XPS foam prevents insects and other pests from penetrating its fabric, which helps maintain the quality and durability of the insulation
Extruded Polystyrene Foam (XPS) is widely used in the construction industry and other sectors due to its unique properties. Below, we will explore some of the most important applications of this foam:
Prominent Features of XPS Foam High Moisture Resistance: One of the standout features of XPS foam is its very high resistance to moisture absorption. The dense and impermeable structure of this foam prevents water from easily penetrating, which helps avoid moisture-related problems and mold in buildings. XPS foam has a closed-cell structure that inhibits the ingress of water and water vapor. This characteristic allows the foam to maintain its performance even in humid conditions and prevents issues such as mold and moisture buildup. With an almost zero water absorption rate, this foam ensures the stability of its thermal performance over a long period.
Extruded polystyrene foam (XPS) has a very low thermal conductivity, typically ranging from 0.035 to 0.045 watts per meter Kelvin. This characteristic means that XPS effectively prevents heat transfer, helping to maintain indoor temperatures at desirable levels. By using XPS foam, temperatures can be optimized during both cold and warm seasons, thus preventing temperature fluctuations. Additionally, XPS contributes to reducing energy consumption; by minimizing the infiltration of heat or cold, it allows heating and cooling systems in buildings to operate less frequently, leading to lower energy costs. Studies have shown that the use of XPS insulation can save up to 50% on energy expenses
Due to the high compressive resistance of XPS foam, this insulation is used in various construction projects, including the insulation of walls, roofs, and floors. Additionally, this foam is utilized as insulation in cold storage facilities and places that require the ability to bear heavy loads. Its capacity to withstand heavy weights and its resistance to deformation under pressure make it an ideal choice for use in demanding conditions.
XPS foam also has good creep resistance, meaning that it does not deform even under constant and prolonged loads. This characteristic is particularly important for projects that require long-term stability.
Long Lifespan, Durability, and Stability: XPS foam, as a thermoplastic material, is highly resistant to environmental and chemical factors. This foam does not deform or degrade when exposed to temperature fluctuations, freeze-thaw cycles, and high humidity. This durability allows XPS foam to maintain its physical and chemical properties for up to 50 years without change
Increased Resident Comfort: By maintaining an appropriate temperature and preventing moisture infiltration, XPS foam contributes to the comfort and well-being of residents. This is especially important during the cold and hot seasons, as it makes the indoor environment more pleasant
Fire Resistance: XPS foam is classified as a fire-retardant insulation material that prevents the spread of fire in the event of a fire. This feature enhances the safety of the building and reduces the risks associated with fire hazards
Easy Installation: XPS foam is designed for quick and straightforward installation. This insulation can be easily cut using simple tools such as a knife or saw, allowing workers to customize pieces to the desired sizes for installation. Additionally, the installation process does not require specialized skills and can be carried out by individuals with minimal experience
XPS foam is typically installed using specialized adhesives or screws. The excellent adhesion of this insulation to various surfaces ensures that the foam remains securely in place and maintains its insulating performance.
Given that the installation of XPS foam is quick and hassle-free, it reduces disruptions in construction processes. Builders can focus more confidently on other stages of the project without worrying about delays caused by insulation installation.
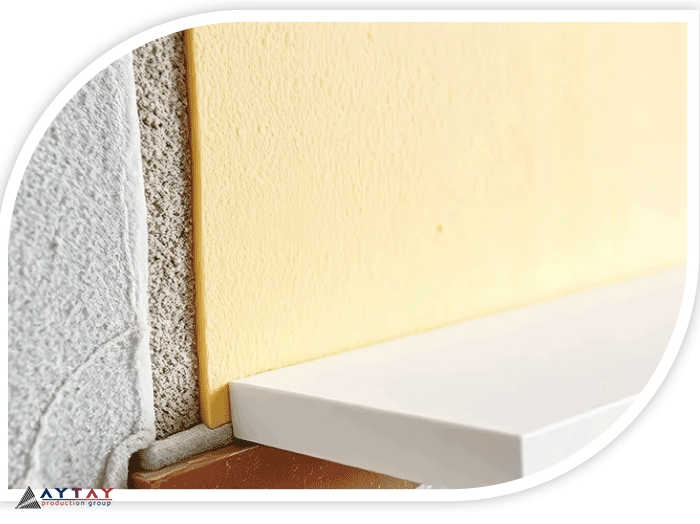
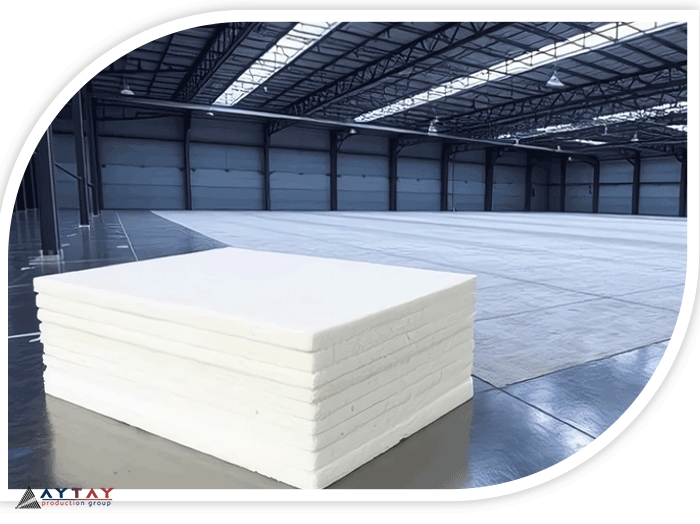
Use of XPS Foam in Industrial and Commercial Projects The use of XPS foam in industrial and commercial projects not only helps reduce energy costs but also enhances the durability and efficiency of structures. Given the outstanding characteristics of this foam, choosing it for insulating buildings is a wise decision that can improve the overall performance of the structure. Aytay Industrial Group, as a reputable manufacturer of XPS foam, provides high-quality products to customers across various industries. This group focuses on the specific needs of projects, producing and supplying different types of XPS foam to the market
How is XPS Foam Produced at Aytay Industrial Group? Selection of Raw Materials:
XPS foam is made from raw materials such as non-expanded polystyrene and specific gases (like R22, CO2, or butane). These materials are carefully selected to provide desirable thermal and mechanical properties for the final product
Extrusion Process:
In this stage, the raw materials are heated and melted. Then, gases are added to the mixture, creating a uniform blend through mixing techniques. This mixture is extruded through a die into sheets of XPS foam.
Shaping and Cooling:
After exiting the die, the foam sheets are rapidly cooled to stabilize their cellular structure. This closed-cell structure provides excellent thermal and moisture insulation properties in XPS foam.
Quality Control:
Aytay Industrial Group conducts rigorous testing on final products to ensure that the produced foam meets international standards and customer requirements. This quality control includes evaluating thermal properties, mechanical strength, and moisture resistance
Advantages of XPS Foam Produced by Aytay
- High Moisture Resistance: Aytay's XPS foam has very low moisture absorption (around 0.2%) and low heat exchange (0.003%), making it an ideal choice for use in humid conditions
- Long Durability: Due to its robust structure, this foam has a longer lifespan compared to other insulations
- Superior Thermal Performance: Aytay's XPS foam has a low thermal conductivity coefficient that helps reduce energy costs
High Quality of XPS Foam Produced at Aytay
Aytay Industrial Group adheres to global standards in producing XPS foam, offering high-quality products with excellent performance that meet diverse customer needs across various industries. This approach not only enhances Aytay's brand reputation but also increases customer satisfaction and strengthens its position in a competitive market.
Types of XPS Foam Produced by Aytay Industrial Group As one of the largest producers of XPS foam in Iran, Aytay Industrial Group manufactures various types of this foam with different thicknesses and features for diverse applications. These foams are widely used in construction, industrial, and commercial projects due to their unique properties.
Standard XPS Foam:
- Thickness: Available in thicknesses ranging from 1.8 to 10 centimeters.
- Application: Suitable for insulating walls, roofs, and floors in residential and commercial buildings.
- Features: This type includes a foil layer that enhances thermal insulation performance.
- Application: Suitable for use in HVAC systems and cold storage insulation.
- Structure: These panels consist of two layers (metal or non-metal) placed over an XPS foam core.
-
- Application: Used in prefabricated walls, industrial and commercial roofs, as well as cold storage insulation.
- Aytay Wall Prefabricated Panels:
- Features: These walls are designed to be ultra-lightweight and fire-resistant.
- Application: Suitable for construction projects requiring quick and efficient installation.
- XPS Foam with Special Features:
Fire-Retardant Types: Depending on project needs, Aytay produces various foams with different resistance features.
Moisture and Heat Resistance: All Aytay products have high resistance against moisture (0.2% moisture absorption) and heat (0.003% heat exchange).
-
Why Are Ayta Products the First Choice for Engineers and Architects? High quality, durability, superior insulation performance, adherence to global standards, and continuous innovation are factors that make Aytay Industrial Group's products the first choice for engineers and architects in construction projects. These features not only ensure customer satisfaction but also elevate the construction industry's standards. Overall, Ayta products are designed to meet diverse project needs—from standard foams for wall and roof insulation to sandwich panels for specific applications—allowing engineers and architects to select the best option for each project. The company has established four specialized production lines for producing compressed foam and XPS insulation with the aim of optimizing energy consumption and implementing Article 19 of national building regulations.
-
Purpose of Establishing Production Lines The primary goal of establishing these production lines is to help reduce energy consumption in the country and enhance insulation standards in buildings. Given the growing demand for high-quality thermal insulations, Ayta utilizes advanced technologies and modern equipment to produce a new generation of XPS foams that not only provide thermal insulation but also possess additional features
Submit Comment